Représentant à elle seule 5 à 7% des émissions mondiales de CO2, l’industrie sidérurgique doit s’engager résolument et durablement à réduire ses émissions.
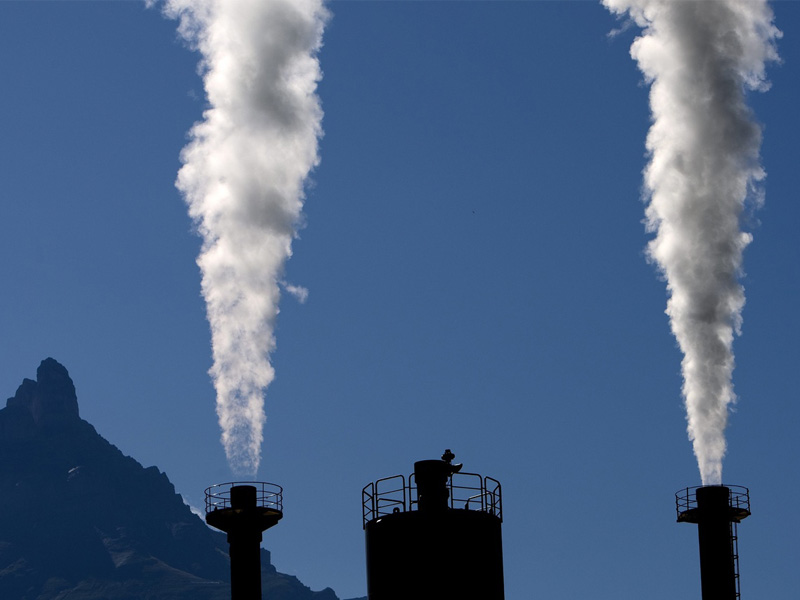
Demande en baisse, surcapacités, volatilité des matières premières affectant les marges, les aciéristes, fragilisés par la crise actuelle utilisent encore des quantités importantes de charbon pour faire fonctionner leurs traditionnels hauts-fourneaux – un procédé particulièrement polluant qui nécessite six cents kilos de charbon pour produire une tonne d’acier. Avec 71% de la production mondiale qui sort encore de ces hauts-fourneaux, l’industrie sidérurgique n’a plus le choix. Représentant à elle seule 5 à 7% des émissions mondiales de CO2 elle doit s’engager résolument et durablement à réduire ses émissions.
Pour tendre vers une sidérurgie sans carbone ou presque, les industriels comptent sur leurs aciéries électriques, la technologie de la réduction directe1, mais aussi sur des innovations de rupture comme la production d’hydrogène «vert»2, voire à plus long terme l’électrolyse du minerai de fer ou la fusion du fer par hydrogène plasma3.
La sidérurgie a commencé à réduire son empreinte carbone grâce au développement de sa filière électrique. Plus récents et représentant près du quart de la production mondiale d’acier (21%), les fours à arc électrique, dont le procédé monte en gamme, se démocratisent. Flexibles, en capacité d’utiliser des produits recyclés comme la ferraille, ces fours, qui participent donc à l’économie circulaire, émettent considérablement moins de CO2 que les hauts-fourneaux (de 3 à 5 fois moins d’après la World Steel Association).
n’est pas encore à ce jour une solution économiquement viable.
Du côté des hauts-fourneaux, l’hydrogène pourrait être la solution pour prolonger leur vie face à l’enjeu de la décarbonation. En effet, remplacer le charbon pulvérisé dans les hauts-fourneaux par de l’hydrogène apparaît comme une solution intéressante à court terme. Celle-ci réduirait les émissions de CO2 de 20 à 30%. Par ailleurs, la capture, le stockage, et dans certains cas la valorisation du CO2 encore émis par ces procédés historiques, pourraient venir renforcer la réduction de leurs émissions.
En revanche, cette solution ne permettra pas aux hauts-fourneaux de s’affranchir totalement d’une consommation de charbon qui restera malgré tout importante. Par ailleurs, le procédé de réduction directe, dont le métal pré-réduit alimente la filière électrique, fonctionne au gaz.
Dès lors, poursuivre la transition de la production, nécessitant majoritairement à l’heure actuelle l’usage de hauts-fourneaux, vers des solutions combinant fours électriques, procédé de réduction directe et hydrogène, constituerait la solution gagnante pour décarboner durablement la sidérurgie. Cette combinaison industrielle innovante a l’immense avantage de nécessiter peu d’énergies fossiles, l’hydrogène pouvant remplacer le gaz au sein du cycle de production.
Néanmoins, cette option industrielle est doublement gourmande en électricité: à la fois pour les besoins énergétiques du four électrique, mais aussi pour produire en amont de l’hydrogène vert sans émission. Cependant, si la production d’électricité est assurée par des sources décarbonées, cette combinaison devient ultra-efficace. Elle permet d’atteindre des émissions de CO2 quasiment nulles en les réduisant de 95%!
Si la faisabilité technique des technologies plus propres utilisant de l’hydrogène est acquise, la promesse de cette sidérurgie verte repose sur l’accès à bas coût de l’hydrogène vert dont le coût de l’électricité associé est aujourd’hui un frein à son développement. Or, la production d’hydrogène vert à grande échelle et à bas coût n’est pas encore à ce jour une solution économiquement viable.
Pour autant, les sidérurgistes voient à long terme et développent dès à présent ces technologies qui pourraient être rentables à partir de 2035, impliquant un recours massif à l’hydrogène, dont la demande pour la sidérurgie devrait être multipliée par dix entre 2030 et 2050.
Si la crise actuelle a fragilisé les sidérurgistes européens, elle leur offre également l’opportunité de se positionner comme les leaders de la production d’acier décarboné.
De nombreux projets sont d’ores et déjà en cours, dont le précurseur suédois HYBRIT créé par l’aciériste SSAB, la compagnie minière LKAB et le fournisseur d’énergie Vattenfall. Ce projet a pour objectif la commercialisation d’acier sans émissions, de l’extraction du minerai jusqu’au produit fini, à horizon 2036 avec la mise au point dès 2026 du premier site pilote. Plusieurs autres sidérurgistes européens lui emboîtent le pas (Salzgitter, Thyssenkrupp, ArcelorMittal, Voestalpine) avec des temps d’adaptation plus longs, car passer à une production décarbonée implique l’abandon du procédé de hauts-fourneaux et en conséquence des investissements massifs à engager dès à présent.
Pour mener à bien la transformation de ces sites européens produisant environ 60 millions de tonnes d’acier chaque année, ArcelorMittal devrait par exemple dépenser 50 milliards d’euros. Et c’est sans compter le coût des infrastructures de production et de transport de l’hydrogène vert, évalué pour l’Europe entre 150 et 200 milliards d’euros.
Pour accélérer cette transition, l’Europe politique guidée par la France et l’Allemagne est passée à l’action: plans de relance, aides spécifiques pour la filière hydrogène, dispositifs européens pour tendre vers un véritable marché de l’acier bas carbone, comme par exemple la taxe carbone aux frontières ou les contrats sur la différence carbone.
Ainsi, la volonté d’une transition technologique est bien là, poussée par des réalités politiques avec l’engagement européen de neutralité carbone en 2050, mais aussi par des considérations économiques avec une filière où la concurrence est rude et où l’anticipation sera vitale sur le long terme.
La récente annonce du leader mondial chinois Baowu de produire de l’acier neutre en carbone d’ici 2035 illustre cette nouvelle course à la neutralité, garante de la compétitivité des sidérurgistes dans une vingtaine d’années!